The Direct Correlation Between Digitized Standard Operating Procedures (SOPs) & Better Quality Performance
Any organization has a variety of tasks to be performed by various departments. These functions intersect at various points and therefore, consistency is essential to minimize confusion. Furthermore, as people move on or move out and newer team members take on the role, they must continue to perform the tasks in expected ways for business continuity. Any change or improvement must be discussed and consensus arrived at before it is implemented, and the impact assessed to ensure it has the desired effect.
With many people from different teams involved, communication and collaboration can be a challenge if a standardized process is not followed by all. Therefore, businesses must put in place standard operating procedures (or SOPs), which provide step-by-step work instructions to the operators to guide them through a task. A well-established and east-to-follow SOP enhances employee efficiency, productivity, and safety of the team. It plays a vital role in improved quality, adherence to processes/approaches, and overall operational effectiveness.
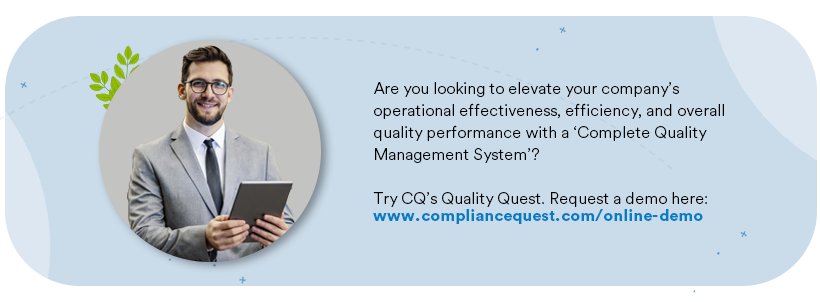
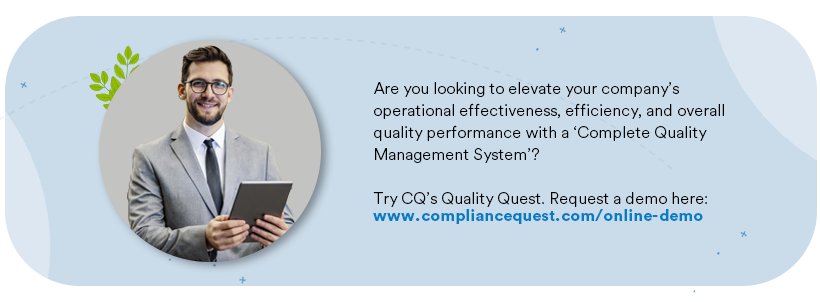
Writing SOPs for ‘The Connected Worker’
The standard operating procedure document is traditionally available in a manual format. Though in today’s world of digitization, it may also be available in electronic format, this is just an extension of the manual document and access can be difficult. As manufacturing industries embrace digital technologies to automate their work processes for greater efficiency and productivity, providing them with digital SOPs is also becoming critical.
Gartner defines the connected factory worker concept as a new approach to industrial efficiency:
“It’s as much a technology construct that changes how factory workers access information and knowledge to do their jobs differently, as it is a change management exercise that is rooted in workforce development, behavioral shifts, and integrated continuous improvement.”
The connected worker uses a variety of technologies such as AR/VR goggles, learning management, and mobile/tablets to augment one's natural abilities. These help to improve productivity and efficiency, identify potential dangers in the workplace, skill up based on need, and enhance the onboarding experience.
As manufacturing SOPs unify different operators to perform the same tasks, streamlining them can enable continuous improvement and increase OEE (Overall Equipment Effectiveness).
However, in spite of great technology adoption, these are some data points to ponder over:
- 13% of business services workers still don’t have access to digital devices while performing their tasks. This is especially true on the factory floor. And, this has compelled many to bring their own devices at work.
- Due to technology issues, including the absence of or improperly functioning devices, 49% of workers lose 10 minutes per hour on average, making them lose three hours a week per worker.
In this context, manual SOPs also limit the ability of workers to refer the SOP to align their tasks every time, which can lead to slip-ups and nonconformance. Apart from connecting workers to all their key tasks, providing access to digital SOPs through mobile-enabled apps can provide the following benefits:
- Improved Compliance: By enabling anytime, anywhere access to digital SOPs, businesses can improve the efficient implementation of SOPs. The operators can use their devices to refer to the policies anytime regardless of the location to improve compliance with the SOPs and policies.
- Easier Communication: Making changes to the Digital SOPs and sharing the revised version is also a matter of clicking the button. The changes need to be made in just one place and will be accessible to any employee in any of the locations through the app. This ensures continuous improvement without disruptions or confusion, or even time lag between introducing the change and implementing it.
- Embedded Visuals: Not only images, even videos can be embedded into the digital SOPs, improving the clarity of how an operation must be performed. This reduces the training time and doubts can be clarified by chat or email, thereby further improving the response times.
- Training on the Go: The access to videos also reduces the need for external consultants and scheduling a specific time to train a batch of workers on the new procedure. It also ensures all operators have access to the same inputs at the same time, thereby reducing disruptions and deviations.


Key Challenges in the SOP Management Process
Despite their advantages, digital SOPs also come with some challenges. These include:
- Updating SOPs: The SOPs can be changed only by people with specialized skills using specific software to handle images and videos
- Cost of Changes: This need for specialized skills and software adds to the cost.
- Absence of Audit Trail: The changes made to the images and videos cannot be traced due to there being no easy audit trail.
- Increased Storage Space: Video files tend to be heavier, and though they make understanding a new procedure easier, they also require a lot more storage space
- Difficulty in Searching for Video Files: In a file heavy with several videos, it can become difficult to locate the specific video one is looking for. It's easier to find a specific step in text than in video.
CQ’s Digital SOP Solution for Effectiveness and Efficiency
CQ's Digital SOPs enable rich content types and graphical process flows that align with the needs and expectations of the modern nimble digital workforce.
Businesses can create a more actionable SOP that is easier to adopt and comprehend by empowering organizations with version control for graphical elements without the need for specialized skills. This shortens the time to value, reduces the cost of implementing changes, and being cloud-based, reduces the need for storage.
By implementing CQ’s digital SOP, businesses can empower their frontline, across shifts, locations, and teams, with the information needed to standardize operations, make changes, and collaborate without delays. This helps to deliver better quality work with knowledgeable and skilled operators who can confidently perform their job functions and increase productivity.
Some of the key features that make CQ digital SOP convenient and cost-effective include:
- Reusability
- Access to relevant data
- Rich text integrated with images and videos
- Interactive Forms
- Link control Docs/Library
Visit www.compliancequest.com for more information on the ComplianceQuest Digital SOP solution and our quality management system to make your operations compliant and efficient.