The 8D Way to Manage Your Corrective/Preventive Action Processes
Key Highlights:
- 8D is an extremely effective, proven problem-solving framework, especially in the manufacturing and automotive sector.
- However, to truly benefit from the 8D approach to CAPA you need a next-generation EQMS tool that offers easy access to data, enables seamless collaboration and brings together systems, people and processes in a single, unified platform.
- ComplianceQuest’s next-generation EQMS platform offers a CAPA software with 8D available out-of-the-box. It makes it easy to automate, streamline and digitalize the entire 8D process.
- Several of the world’s leading manufacturing companies have used CQ CAPA software to reduce the cost of quality and use AI and data to spot issues and drive investigations.
The Eight Disciplines of Problem-solving (8D), first introduced by Ford Motor Company in the 1980s as Team Oriented Problem Solving (TOPS), is an effective framework for finding solutions. It helps in identifying the root cause of any problem, implementing a short-term fix, and also creating a long-term solution to prevent a recurrence.
While it is extremely popular in the automotive and manufacturing industries, 8D has become a preferred method for problem-solving for quality engineers and other professionals across segments such as healthcare, retail, finance, government, and manufacturing.
The 8D methodology helps identify, correct, and eliminate recurring problems, making it useful for both product and process improvements.
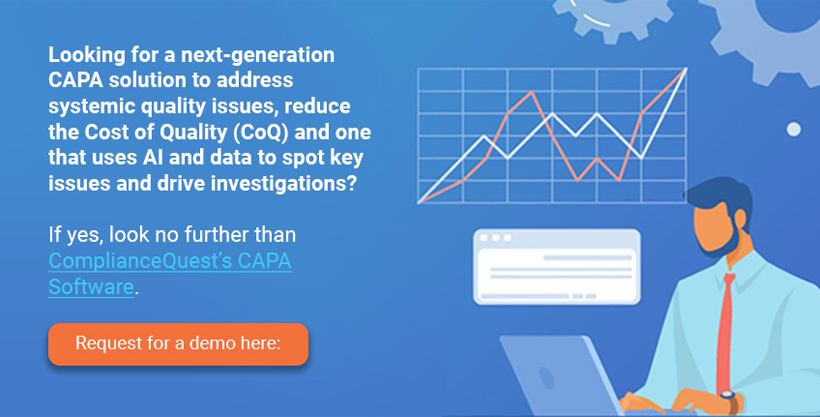
The 8D problem-solving model uses statistical analysis to identify root causes and identify a corrective action/preventive action. It begins with D0, which is the planning stage, and then proceeds to:
- D1: Establishing a team with product/process knowledge
- D2: Defining the problem and enabling quantification using the 5W2H approach–who, what, where, when, why, how, and how many
- D3: Developing a short-term response
- D4: Identify the root causes and verify them
- D5: Identify long-term solutions and quantitatively prove their effectiveness
- D6: Implement and validate corrective actions
- D7: Prevent recurrence by modifying the management systems, operation systems, practices, and procedures
- D8: Recognize the team’s collective effort in resolving the issue
4 Reasons Why You Need to Automate and Digitalize the 8D Process
In the 1980s and 1990s, the 8D process could be conducted manually due to less complexity in processes. But today, globalization has led to the outsourcing of the manufacturing process with a globally spread out supply chain.
Challenge #1 – The 8D team could be drawn from members spread across different geographies. To bring product and process experts to one location can disrupt work and lead to loss of productivity, not to mention the associated costs. It is key to running an 8D process with the right tools and data at your fingertips. The digital tool used must enable ease of collaboration, documentation and brainstorming.
Challenge #2 – The interdependence of processes requires greater visibility into the impact of a change upstream and downstream. For instance, a change introduced in one process will affect a process downstream or may require some changes to be made upstream for the required change to be effective. Therefore, verifying this manually can be limiting and prone to errors.
Challenge #3 – Maintaining effective communication between the participants as well as with the rest of the organization is crucial for the successful implementation of findings after 8D analysis. With people working in different time zones and with different priorities, making sure all are aligned to the new requirements can become difficult.
Challenge #4 – Documentation of the CAPA process is a regulatory requirement. However, in a manual 8D approach, documentation can be complicated, incomplete, and updating and maintaining it can be time-consuming and costly.
FDA/ISO Requirements: The Need for Verification After Implementation
While 8D stresses on verification of corrective actions before implementation, FDA and ISO regulations governing CAPA, require manufacturers to demonstrate the efficiency of CAPA after it was implemented.
Points 3 and 4 of 21 CFR 820.100, for instance, states that the CAPA actions implemented for nonconformance and other quality problems need to be verified or validated to ensure their effectiveness and that they do not adversely affect the finished device.
ISO 13485:2016 – 8.5.2 Corrective action also lays down
- The need for planning and documentation
- Verifying that the corrective action does not adversely affect the performance of the medical device and meets applicable regulatory requirements
- Reviewing for its effectiveness
This requires data to be collected over a period of time, depending on the volume of production, and then it is analyzed for its effectiveness and conformance.
CAPA effectiveness check has to be based on key performance indicators and requires:
- Establishment of benchmarks using quantitative data collected during the root cause analysis
- Verifying performance following the implementation of the corrective actions and measuring the success in reducing or eliminating the quality issue or nonconformance
- Performing a process re-validation ensuring that the validation processes include qualitative acceptance criteria for success
Automate 8D Workflows with ComplianceQuest
The cloud-based EQMS from ComplianceQuest is designed to align your processes with industry standards and regulations such as ISO and FDA. Our CAPA Solution, is tailored for problem-solving and intuitively integrates the 8D approach to effectively manage your Corrective And Preventive Action (CAPA) processes and drive Continuous Improvement (CI).
The CQ solution facilitates collaboration between experts located in remote locations, enables easy communication/brainstorming, and captures discussions and findings into documents and records that can be shared within the group as well as the rest of the organization, as needed.
With CQ CAPA Management Software, you can do root cause analysis, detect trends, conduct or link to an existing investigation and root cause analysis, define action plans to change or improve, and ensure effectiveness checks with a structured verification and closure.
The solution integrates with enterprise-wide systems such as ERP and CRM to provide a holistic view of processes across the lifecycle and access to real-time data for effective monitoring and tracking. The EQMS also offers a Change Management solution to manage changes and ensure performance.
The foundation blocks and a built-in workflow indicator of the CAPA solution from ComplianceQuest facilitate the adoption of various problem-solving approaches such as the 8D model, World Class Manufacturing (WCM), and 5W2H.
One of the key elements is the Effectiveness Verification and Closure feature that tracks the effectiveness of the CAPA action and closure of CAPA once it is proven.
Here’s what Lia Budiman of Continental Contitech said about using ComplianceQuest to automate various quality and compliance processes:
“Great product, support, and people to work with!
We have rolled-out CQ across our company to automate various elements of QMS requirements such as Document Management, Complaints, Non-conformances, Corrective Action (8D and A3), Supplier Management and Audit Management. We have been using the software for more than 2 years. We are glad to see how well the system is being used across the company. We have several thousand users on the system currently and working to scale the usage further. CQ solution has been configured to meet our needs, works elegantly across languages, across time zones, and business verticals. With the integration between CQ and SAP to exchange critical data, the process automation provides a lot of productivity.
CQ configuration team and support have worked hard to ensure that our needs continue to be met. They consistently go above and beyond. We cannot be more pleased with our use of CQ QMS capabilities and would definitely recommend to anyone who is looking for a modern cloud-based EQMS solution especially if you want a scalable EQMS solution.”
To know more about how you can leverage ComplianceQuest’s CAPA Management Solution for your 8D problem-solving needs, request a demo here: https://www.compliancequest.com/online-demo/